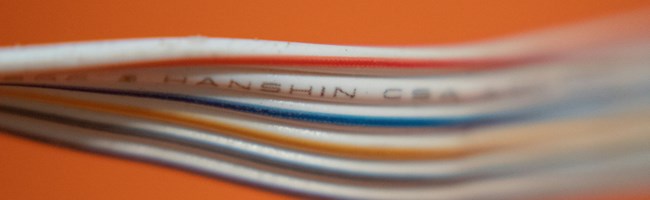
New estimation methods prolong sensor durability
New methods shall estimate the temperature drifts of thermocouples to avoid the need for replacement of sensors or at least prolong replacement intervals.
A thermocouple comprises two dissimilar metal wires joined together at one end to form a measurement junction. A voltage is developed across the wires that is measured at the open end, and which is a function of the temperature gradient between the two ends. Thermocouples made of platinum and its alloys with rhodium are widely used in high value manufacturing applications as they offer relatively high thermoelectric stability in comparison with other thermocouples.
The principal cause of instability, and therefore calibration drift, is vaporization of platinum and rhodium oxides from the wires, which causes a local change in composition. This in turn changes the thermal voltage (EMF) generated for a given temperature gradient, which results in a temperature measurement error because the EMF is different to the EMF that would have been generated during the original calibration for the same temperature gradient.
The use of a multi-wire sensor, considered as a network of thermocouples comprising different pairs of wires and exposed to the same temperature gradient (see the schematic below), offers the possibility to estimate the temperature drift of the individual thermocouples.
New methods for estimating the drift of thermocouples.
The FunSNM project group is developing methods to estimate the temperature drifts to avoid the need for costly and time-consuming replacement of sensors or at least prolong replacement intervals. One of the methods is a physics-based model of the mechanism of vaporization of platinum and rhodium oxides. Another is based on modelling the measured EMF-data recorded by the different thermocouples supplemented with constraints derived from the physics-based model or from empirical considerations (a hybrid approach), and a third method is a purely data-driven approach that uses an empirical model for the relationship between the measured temperature drift data for different thermocouples.
Finally, a simulation of the data recorded by a multi-wire sensor has been implemented and the data generated from that used to train a neural network for estimating the drift.
Schematic of a five-wire thermocouple assembly. The voltage can be measured across any two wires to make an individual thermocouple. All thermocouples are measuring the same temperature because they share a common measurement junction.
The indicated temperature of selected thermocouples from the ensemble, clearly illustrating the calibration drift.
Future work will consider the design of such multi-wire sensors to balance the quality of the drift estimates against the cost of the fabrication of the sensor, the extension of the methods to sensors comprising wires made of cheaper base metals (such as nickel, chromium, and aluminium), and the estimation of the drift of sensors that are spatially distributed within a temperature-controlled environment. The consortium is liaising closely with stakeholders in the aerospace and other supply chains to provide real-world data that can be used to test the methods.